Molds play a pivotal role in various casting processes across industries including automotive, aerospace, art, and even jewelry. A mold serves as a negative impression of the desired object, allowing molten material to be poured or injected into it to replicate the original shape. Traditionally, molds were crafted using labor-intensive methods like CNC machining, manual sculpting, and pattern making. Because these methods often lead to limitations in design complexity and longer lead times, 3D printing has stepped in to fill a major role in helping to speed up the process of creating molds, as well as to increase the scope of possibilities for new designs.
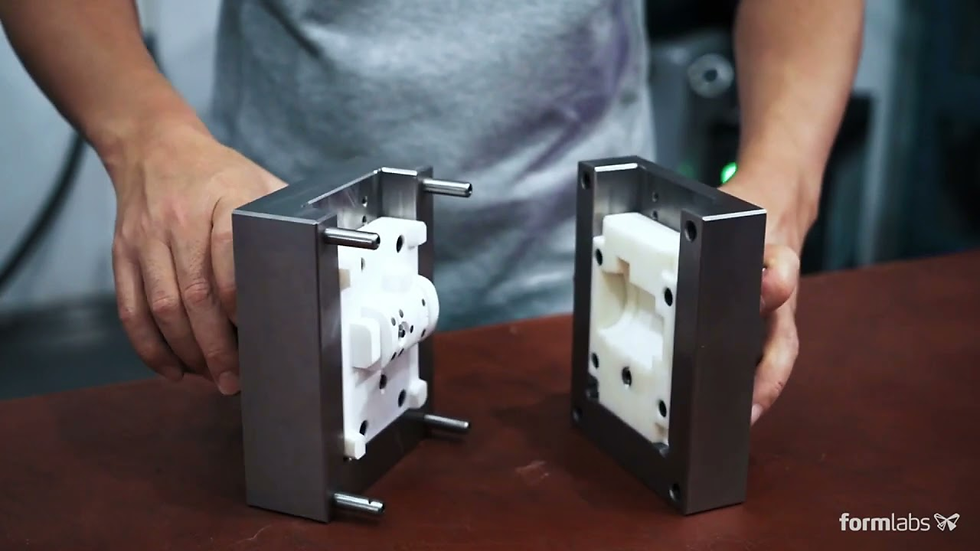
In addition to the design flexibility, cost effectiveness and rapid prototyping, 3D printing offers another advantage to the casting process which has to do with the time it takes for the part to cool and set. Because 3D printing enables the creation of molds with intricate cooling channels that improve heat dissipation, cycle times can be reduced, enhancing the overall speed of the casting process.
Techniques for 3D-Printed Molds
Depending on what is needed for a specific project, several 3D printing techniques can be employed to create molds for casting processes.
Fused Deposition Modeling (FDM): FDM, a widely used technique, involves extruding thermoplastic materials layer by layer. While FDM is cost-effective and offers a range of material options, it might have limitations in achieving fine surface finishes for highly detailed molds.
Stereolithography (SLA): SLA utilizes photopolymerization to create high-resolution molds with exceptional surface quality. This technique is particularly suitable for intricate and small-scale molds.
Selective Laser Sintering (SLS): SLS employs a laser to sinter powdered materials, such as metals or ceramics. It is ideal for creating molds that can withstand high-temperature casting processes.
Binder Jetting: Binder jetting combines powdered material such as sand and a liquid binder to create molds layer by layer, a process known for its speed and versatility, supporting a wide range of materials. This article details a few of the major players (including the US Navy) using sand molds for their casting processes.
Because of the complex regulations in the major industries turning toward 3D printing solutions, 3D printing mold castings can help to avoid the need to recertify, whereas printing parts directly would make intensive certifications necessary. This is a huge advantage, blending traditional metal casting and innovative solutions to create massive advances in efficiency and cost.
Comments